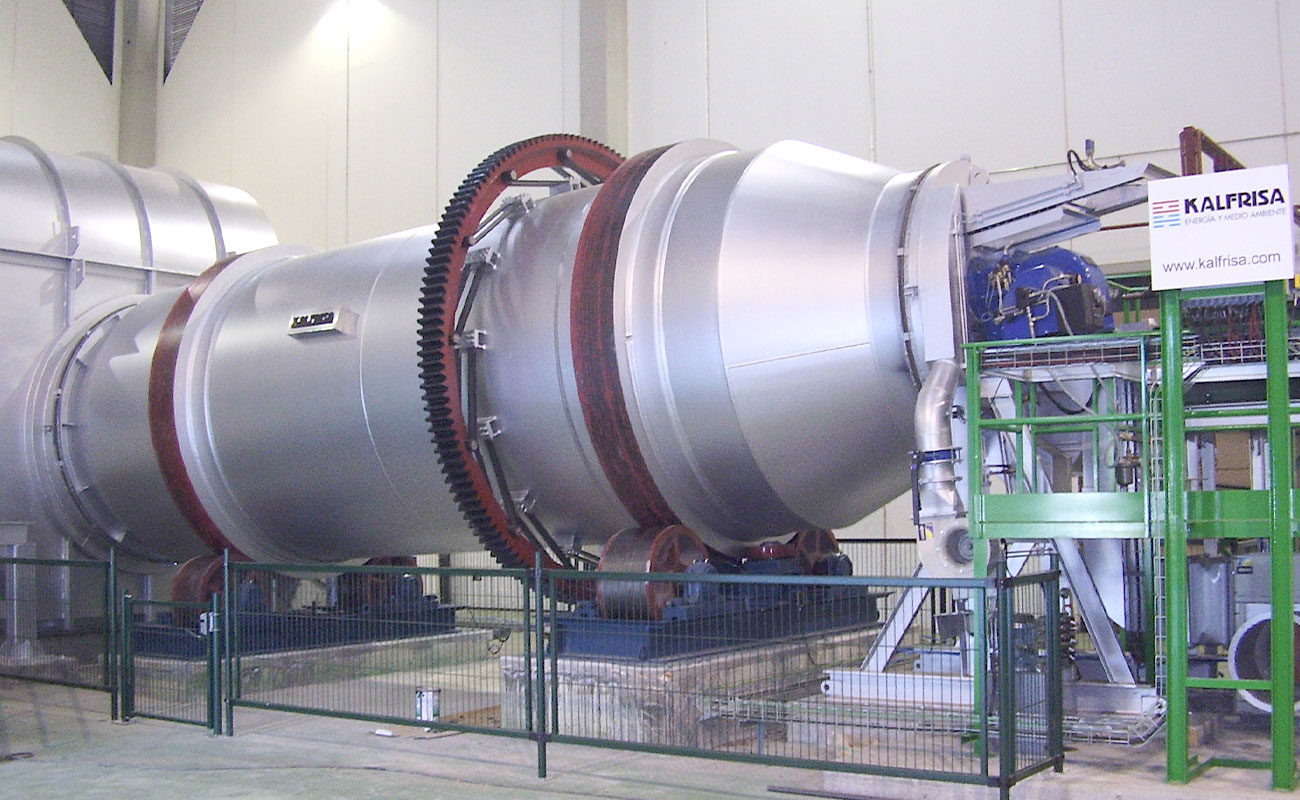
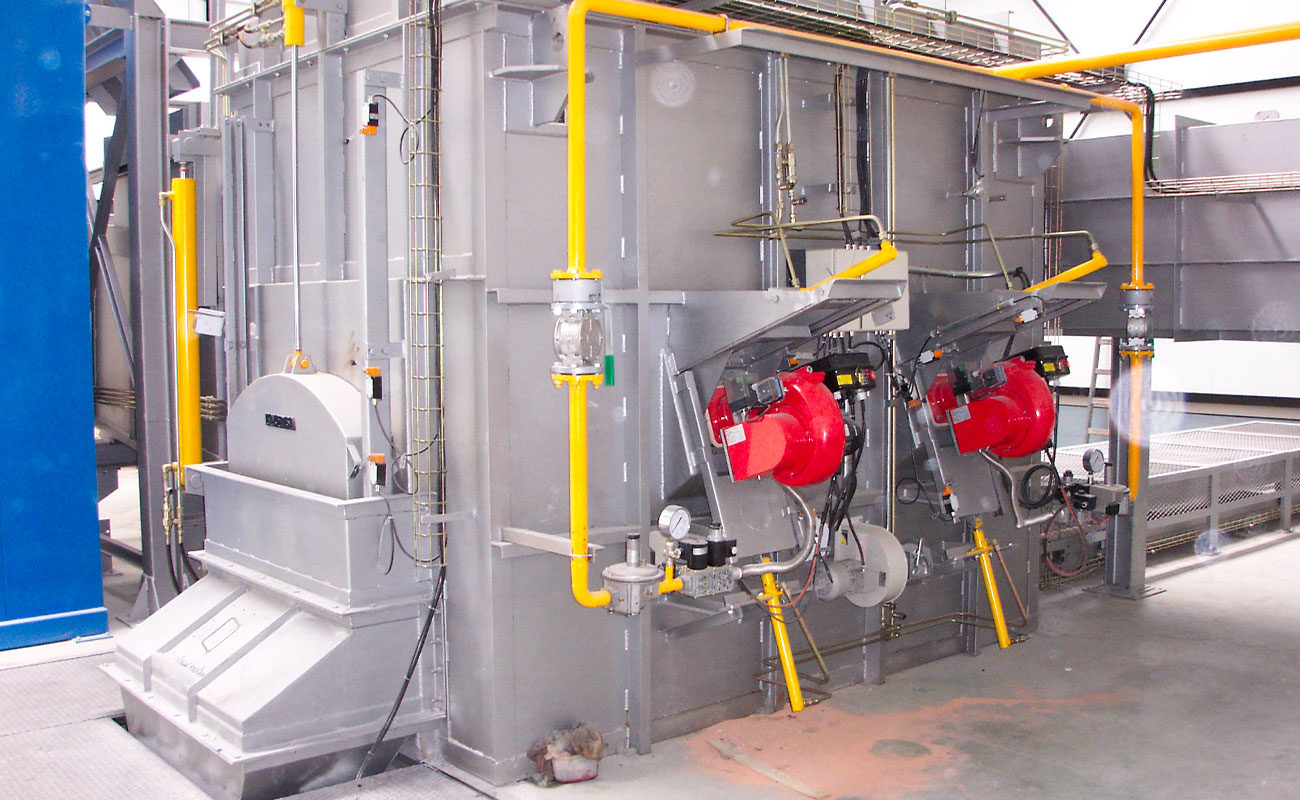
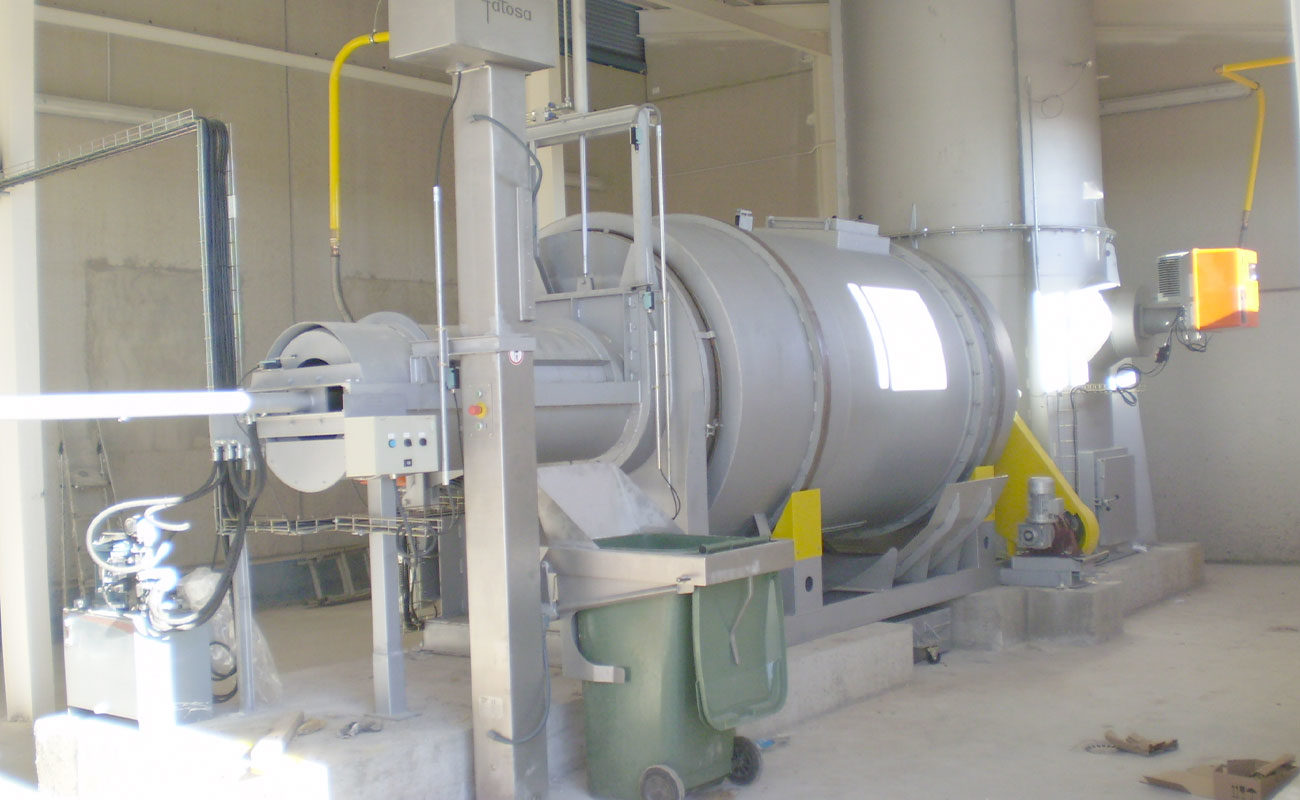
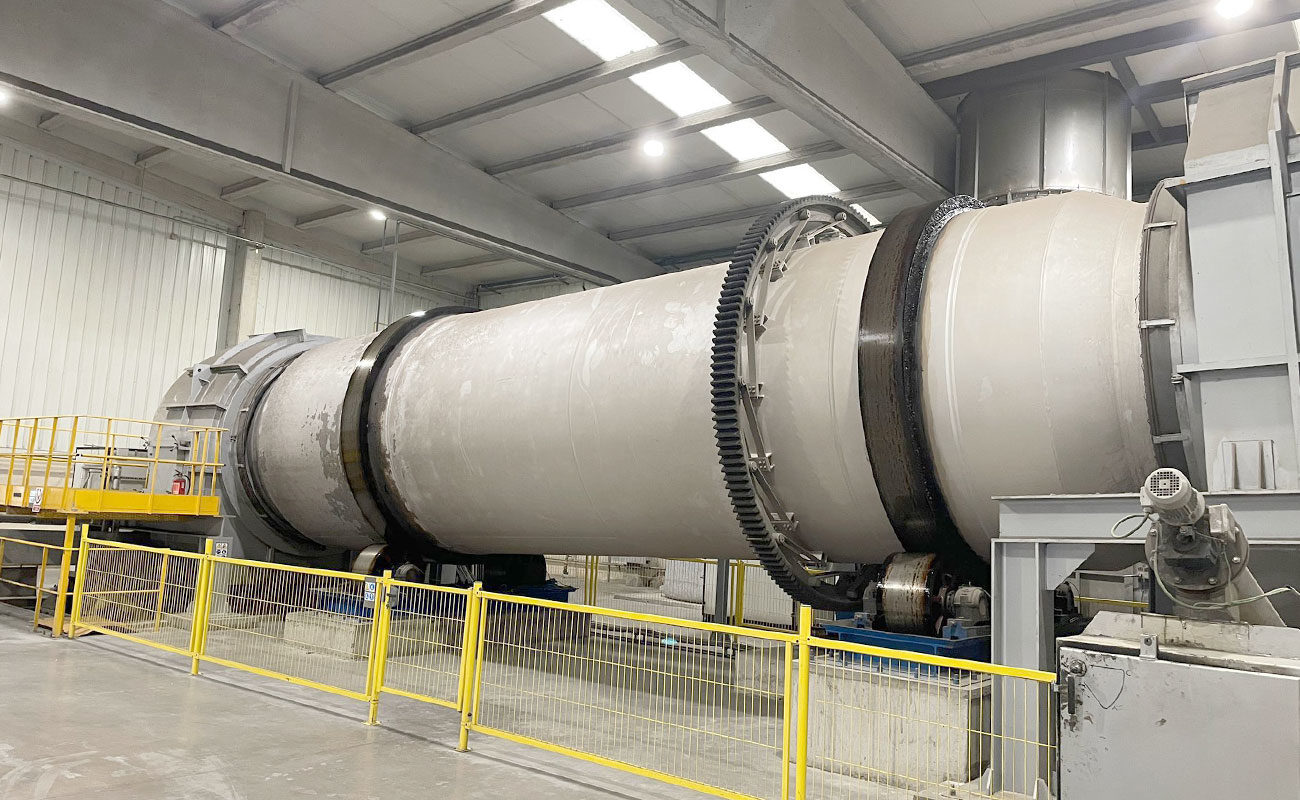
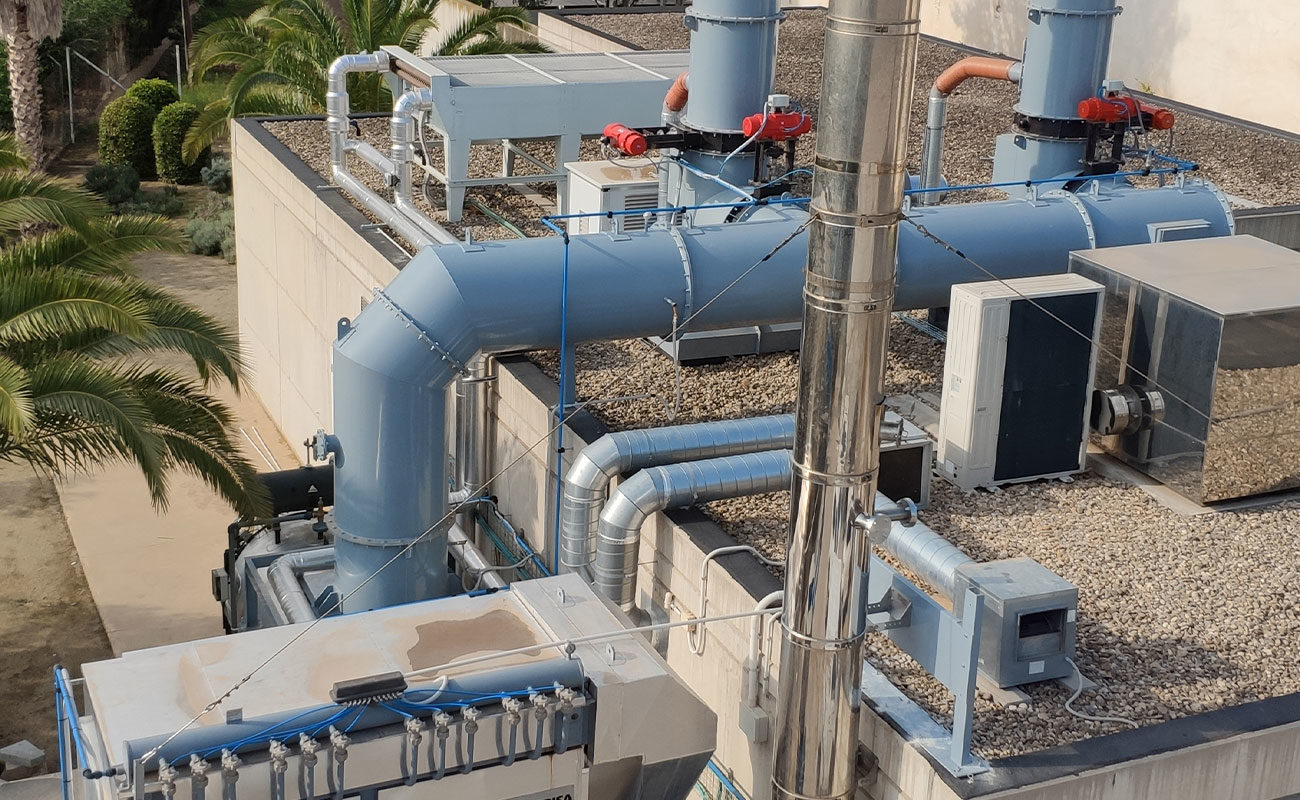
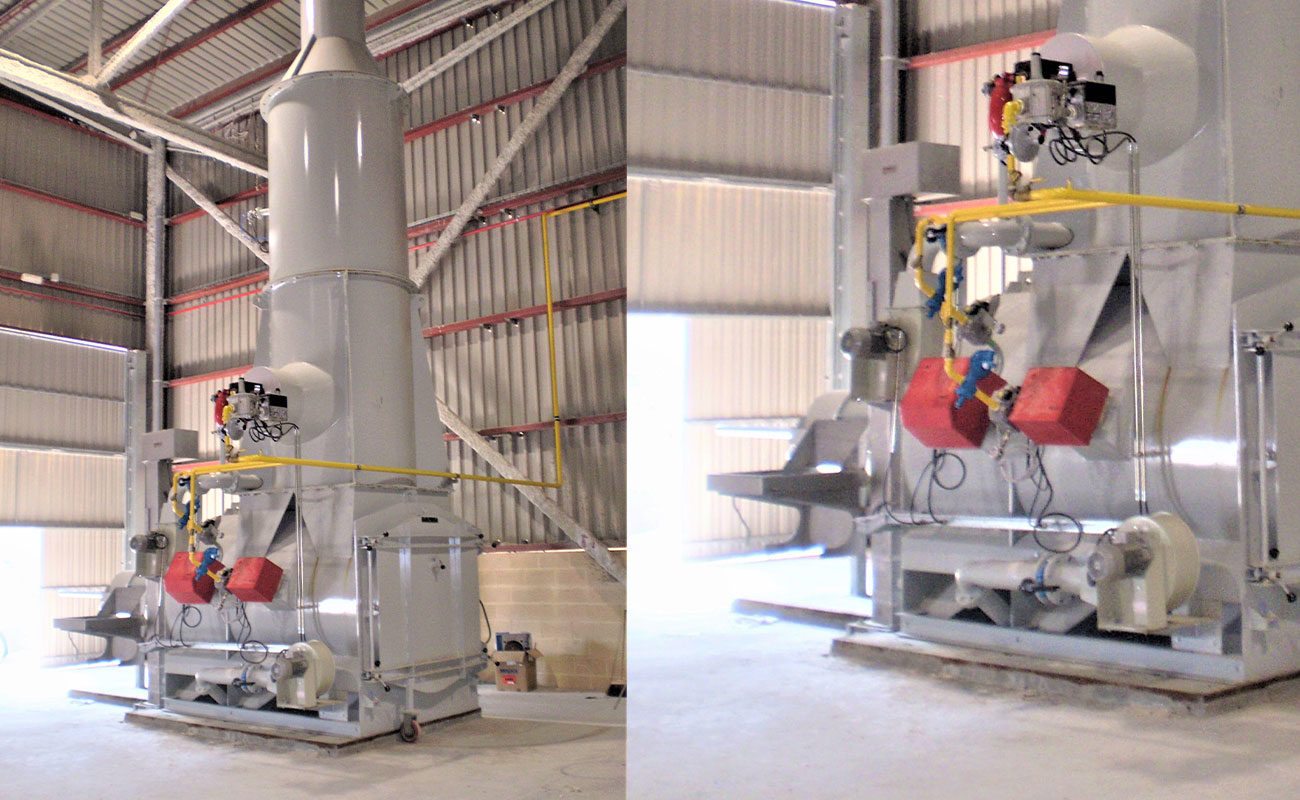
INDUSTRIAL WASTE
Incineration of this type of waste allows a great reduction of the volume of waste. The ash generated constitutes around 5-10% of the initial volume. This allows greater performance by landfills, avoiding the serious saturation problems existing today.
The furnaces have a combustion chamber where the waste is reduced to ash thanks to the action of the burners. A second combustion chamber thermally purifies the gases during a minimum of 2 seconds at 850 – 1100ºC in accordance with current regulations, thereby achieving total oxidation of the gases eliminating odours and making them totally transparent.
Depending on the nature of the waste, it may be classified as hazardous or non-hazardous waste. Depending on it is are classified, the ash from the incineration may be taken to a common landfill or must be taken to a controlled landfill. Additionally, in case of being hazardous waste, the furnace must be accompanied by a gas treatment following incineration. (chemical purification of gases, filters, etc.).
The automated control system of our furnaces controls the operation of the burners and the air distribution valves based on a continuous measurement of pressure, temperature and oxygen, adapting the incineration process as necessary at all times.
For all our furnaces we offer a comprehensive technical assistance and support service, continuous maintenance service and remote assistance.
Fields of application
- Landfills
- Ports, airports and logistics centres for goods
- Companies dedicated to waste management
- Environmental Project engineering
- Chemical industries and the Oil & Gas sector
- Industrial operations in remote or difficult to access places
- Temporary camps and settlements
Accessories
The installation of the incineration furnace can be completed with a system for destroying liquid waste, a heat recovery system and a chemical purification system for gases.
MODELS
KT static furnaces
The range of KT static furnaces has been designed for easily eliminated waste (paper, cardboard, woods, textiles, MSW and light plastics). With horizontal, automated or manual loading. These furnaces have been calculated for destruction of waste with the greatest possible performance.
KT-1.500 | KT-4.000 | KT-8.000 | KT-12.000 | |
Destruction capacity (kg/h) | 50 – 100 | 100 – 200 | 200 – 350 | 350 – 500 |
Chamber volume (m³) | 1,5 | 4 | 8 | 12 |
Maximum loading capacity in the chamber (kg) | 250 | 600 | 1.200 | 1.800 |
ROT range rotating furnaces
The rotating furnaces of the ROT range are prepared for the destruction of waste which is difficult to eliminate, which requires more mixing during incineration. This type of furnace requires stoppage and emptying of the ash at the end of the workday. Designed for a very heterogeneous mixture of waste.
ROT – 600 | ROT – 1500 | ROT-2500 | |
Destruction capacity (kg/h) | 80 – 150 | 150 – 300 | 300 – 450 |
Chamber volume (m³) | 3 | 7 | 12 |
Maximum loading capacity in the chamber (kg) | 300 | 600 | 1.000 |
KRL furnaces
The KRL range of furnaces are rotating furnaces which have a continuous ash extraction system, which allows them to operate 24/7 without needing stoppage for cleaning, in contrast to the ROT range. Like the ROT range, they are designed for the destruction of heterogeneous mixtures of waste which are difficult to incinerate.
KRL – 1 | KRL – 2 | |
Destruction capacity (kg/h) | 250 – 300 | 300 – 500 |
Chamber volume (m³) | 12 | 15 |
Maximum loading capacity in the chamber (kg) | 600 | 1.000 |
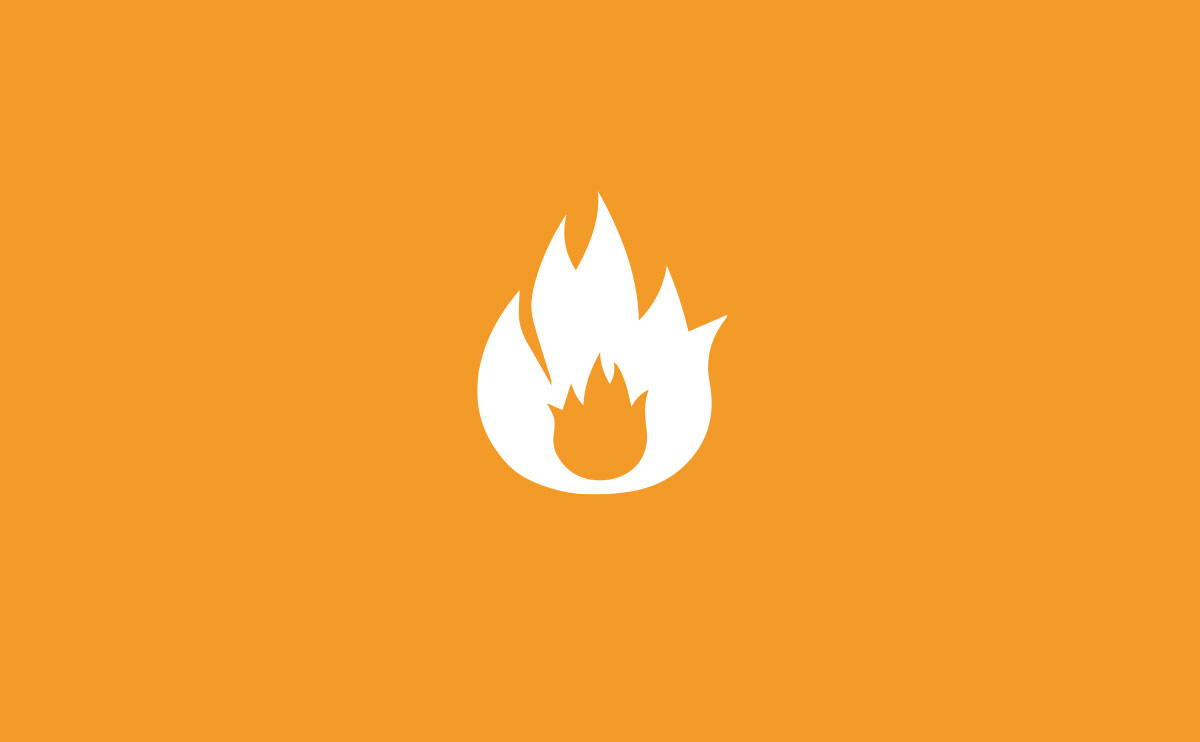
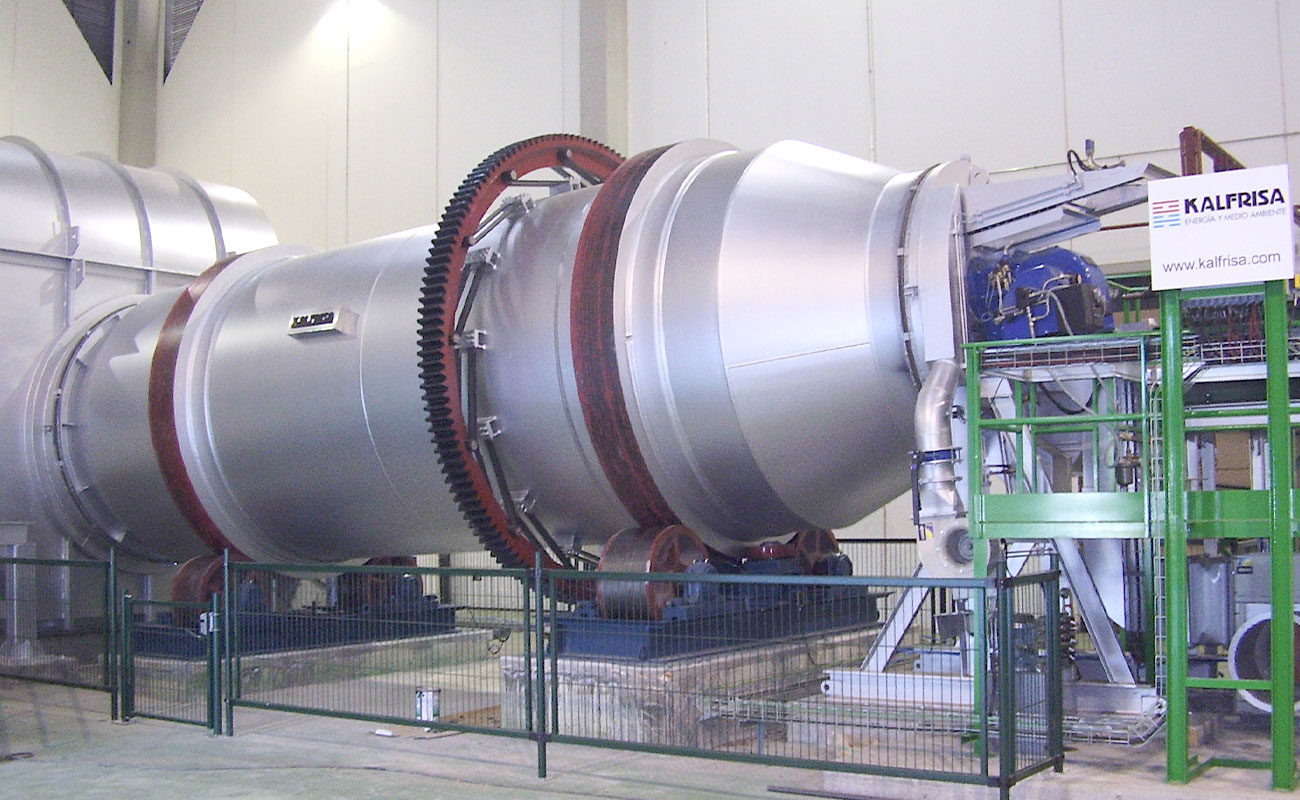
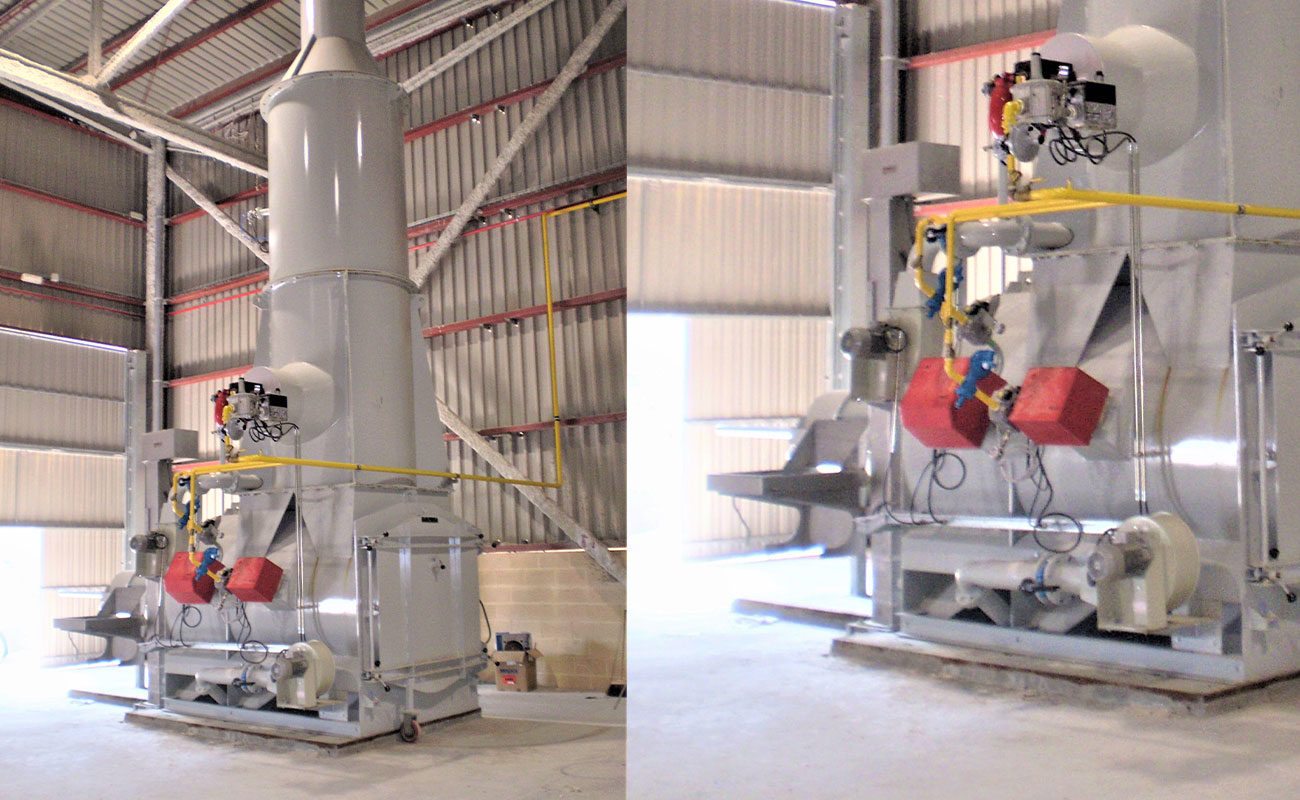
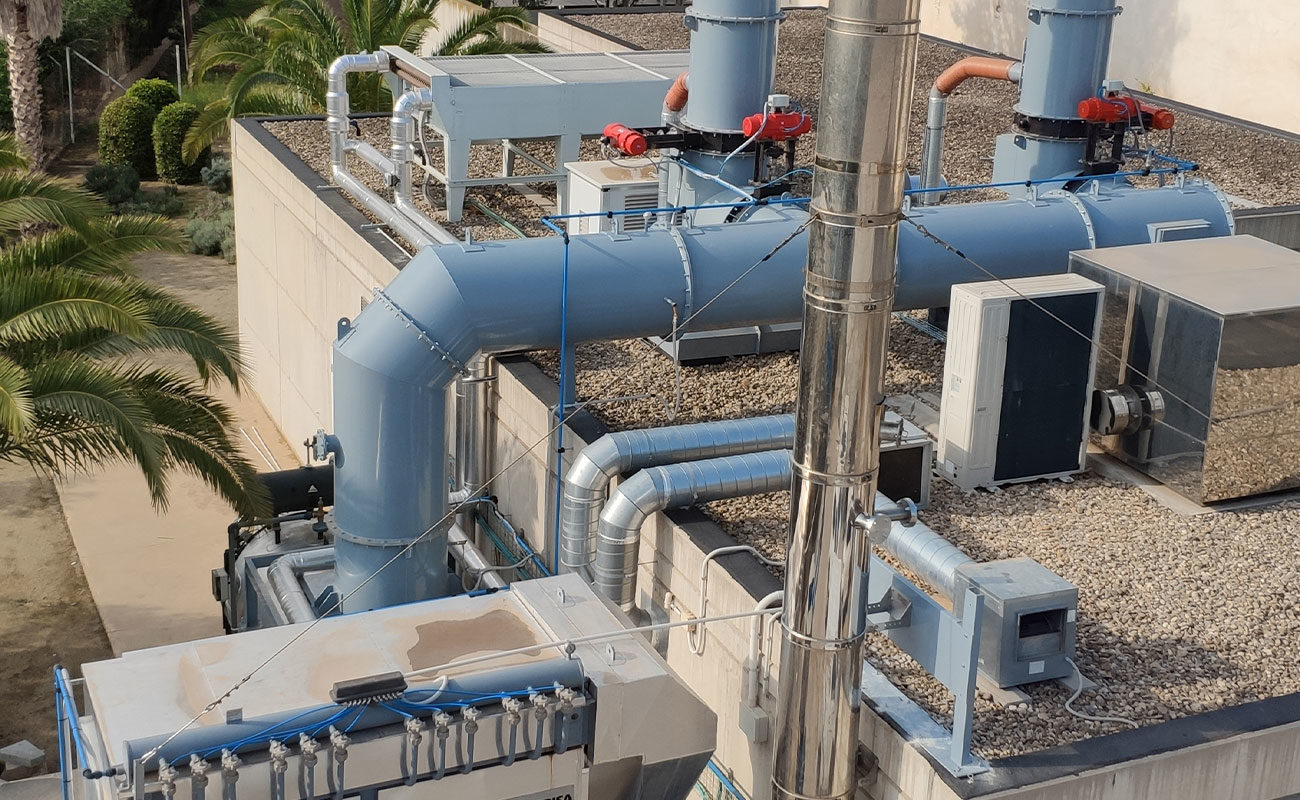
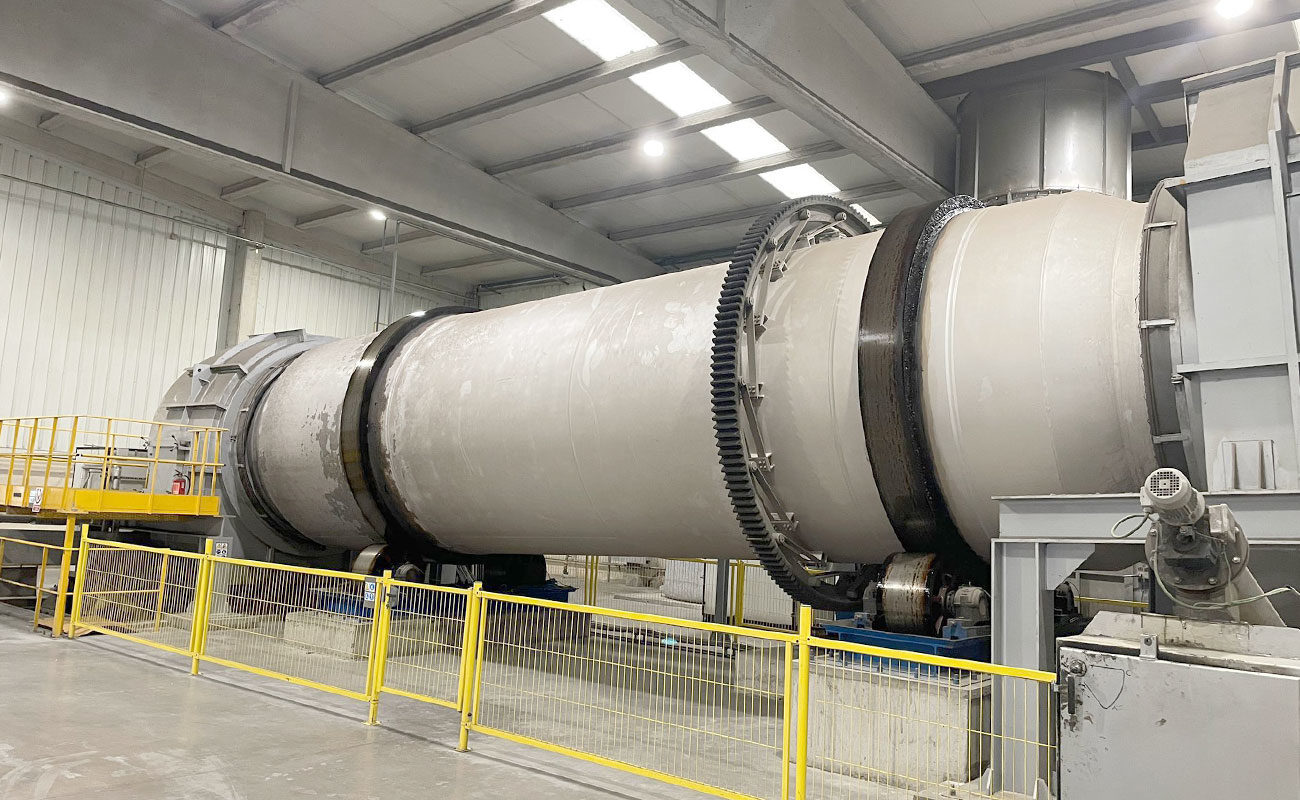
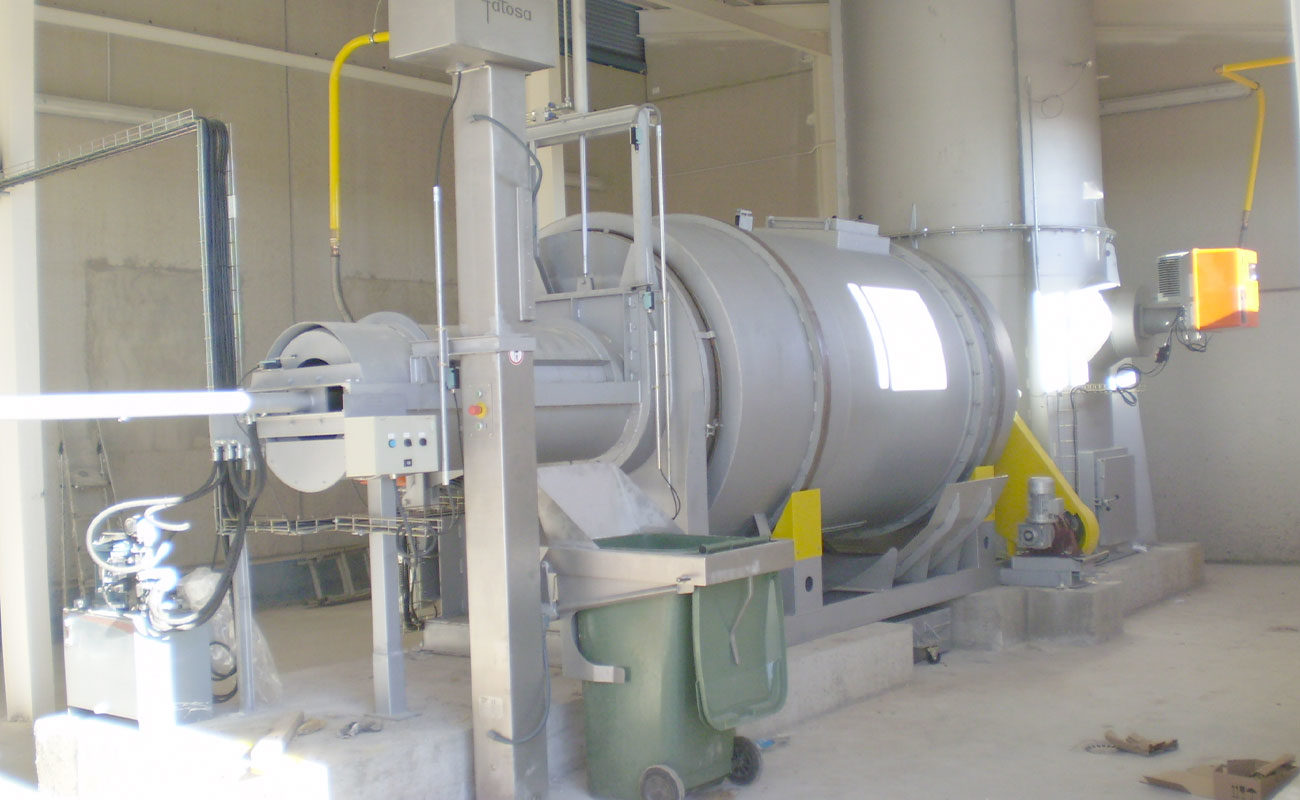
Destruction of liquid waste.
An injection lance can be installed in any of the chambers of the furnace, this system spraying a liquid waste inside the furnace to be incinerated. Along with the lance, an air compressor and the whole pumping system is installed in a cabinet in a location near the furnace.
The liquid to be input must be previously filtered. This waste must be pumpable; for example, the most common forms of this type of waste are: oils, contaminated water, solvents, distillation tails, etc.
The destruction capacity with depend on the LCV of the liquid waste to be eliminated.
Heat recovery.
The incineration generates gases at 850 or 1100ºC depending on the type of waste and local regulations in effect. This whole volume of gases can be made to pass through different devices to recover thermal energy from the process. The recovery methods are as follows:
- Generation of hot water through recovery boiler.
- Generation of steam through saturated steam boilers.
- Generation of hot air through Gas – Air exchangers.
Chemical purification of gases
Depending on the applicable regulations and the nature of the waste, gas purification systems can be included to neutralise acid gases, dioxins and other components which are harmful to health. The purification components used most are:
- Dry channel: Addition of Sodium Bicarbonate (NaHCO3) and activated carbon to the flow of gases + sleeve filter.
- Semi-wet channel: Addition of Lime (Ca(OH)2) and activated carbon to the flow of gases + sleeve filter.
- Wet channel: Wet scrubber with addition of Lime + sleeve filter.
These purification systems are based on a reaction of the acid gases with the base additives to generate steam and salt crystals. Additionally, the activated carbon absorbs the particles of dioxins, furans and heavy metals on its surface.
All these particles, along with the excess of reagents, are made to pass through a sleeve filter where a filter fabric retains all the particles.
Finally, the gases released to the atmosphere have previously been treated and filtered, therefore complying with current regulations.