Kalfrisa reference manufacturers of Heat Recovery Systems
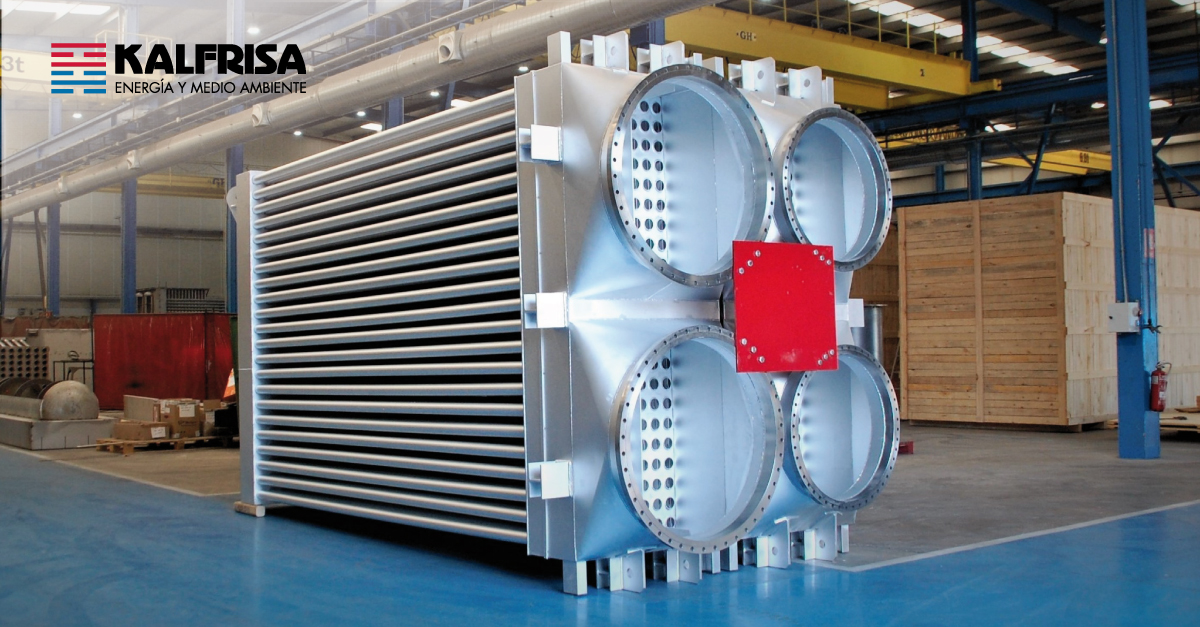
Our equipment uses the outgoing heat from the reheating/treatment furnaces to preheat the combustion air required in the furnace burners themselves.
In this way, part of the outgoing energy is reintroduced into the system and the fuel required is significantly reduced, with a consequent reduction in greenhouse gas emissions.
Our customers are well aware of this, yet sometimes they don’t realize how much extra fuel they are wasting and how much money they are throwing down the chimney by not having a Heat Recovery optimized for your process.
A few days ago, a customer told us that if the ROI of a piece of equipment we were offering was longer than 1 year, he would probably have problems to get the investment due to company policy.
The recovery is installed in a treatment furnace that consumes about 600.600,000/month in natural gas and that replaces a previous one of which we were told “it is not completely broken, we do not believe that there are reasons to change it yet”.
In short, the difference in fuel savings between the old “not quite broken” equipment and a new one was 10%, implying a difference in savings of 60,000 euros per month, about 700,000 euros per year. And the recuperator was bid for exactly €60,000.
Therefore, the ROI of the equipment was not that it did not exceed one year, it was that it was barely one month and when the person in charge of the oven found out, it changed from “there was no reason to change it” to “why didn’t we change it before”.
A few years ago the Heat Recovery Units used to be changed when they were broken, after 10 or 15 years, now it is IMPRESSIVE to check if each one of the equipment is giving the maximum performance because with payback times of few months the investment is mandatory.
Not only can we be wasting money on fuel, but it is everyone’s job to reduce the environmental impact of an industry as critical and necessary as steel.