Fields of application
- Elimination of organic components, including mercaptans, terpenes and SH2.
- Elimination of organic aerosols, such as from coffee roasting, drying furnaces, etc.
- Purification of VOCs from solvent application processes
- Industrial processes of painting parts
- Chemical, pharmaceutical and resin manufacture industries
- Printing and flexography industries
- Food industry
- Industries which produce unpleasant odours
- Manufacture of plastics
- Lamination of wood
Advantages
- High destruction efficiency.
- Wide range of flows to treat and concentration of contaminants.
- Wide field of application in terms of type of contaminants.
- Ease of operation.
- Possibility of energy recovery of gaseous waste.
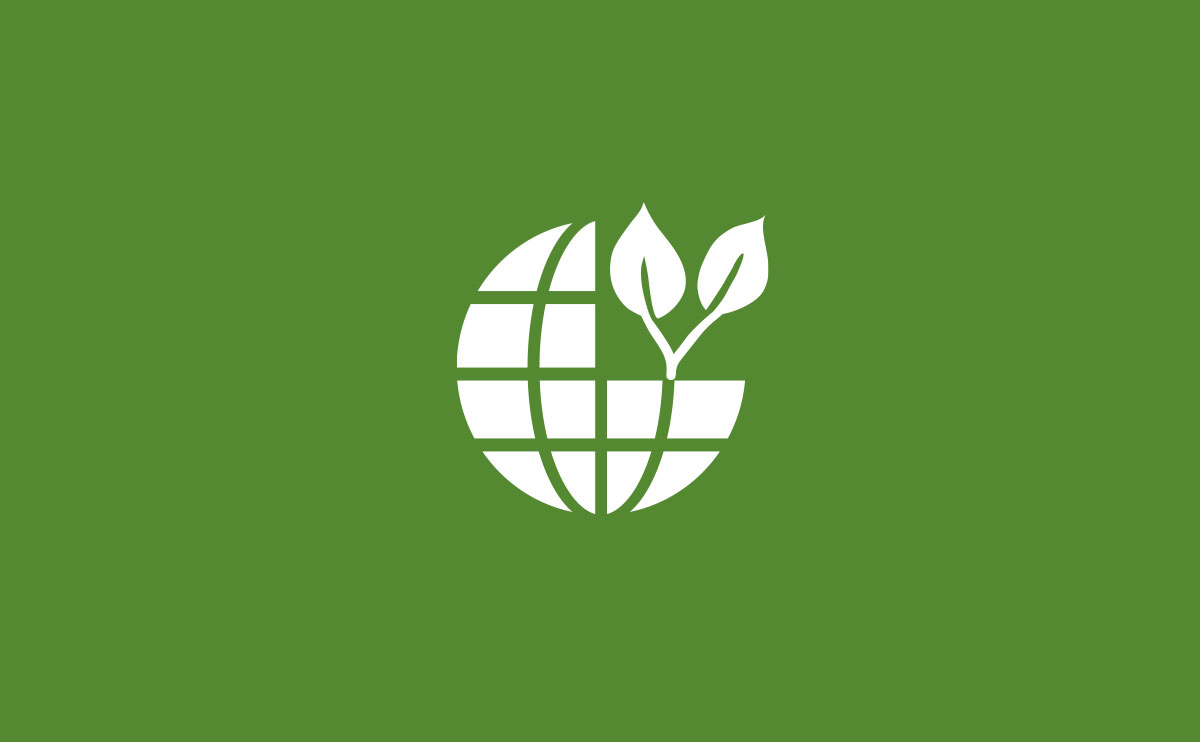
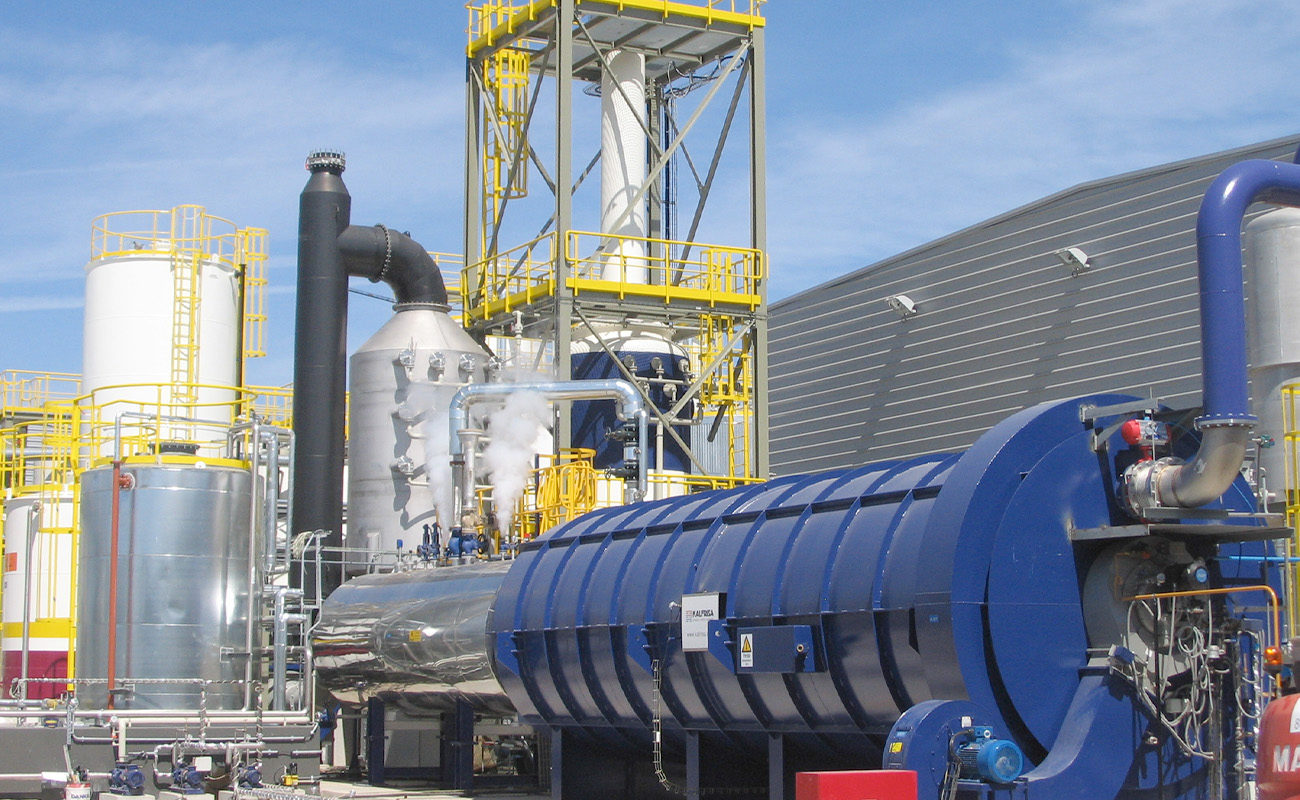
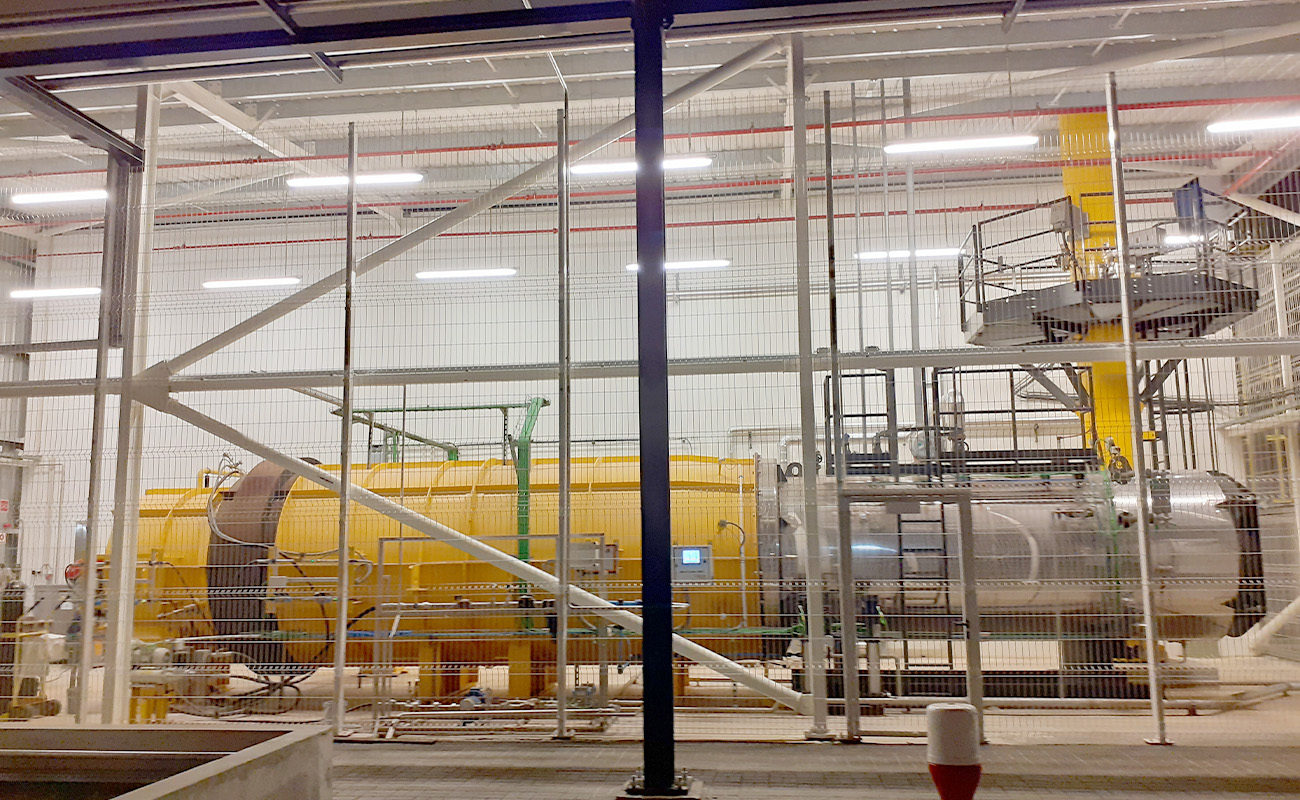
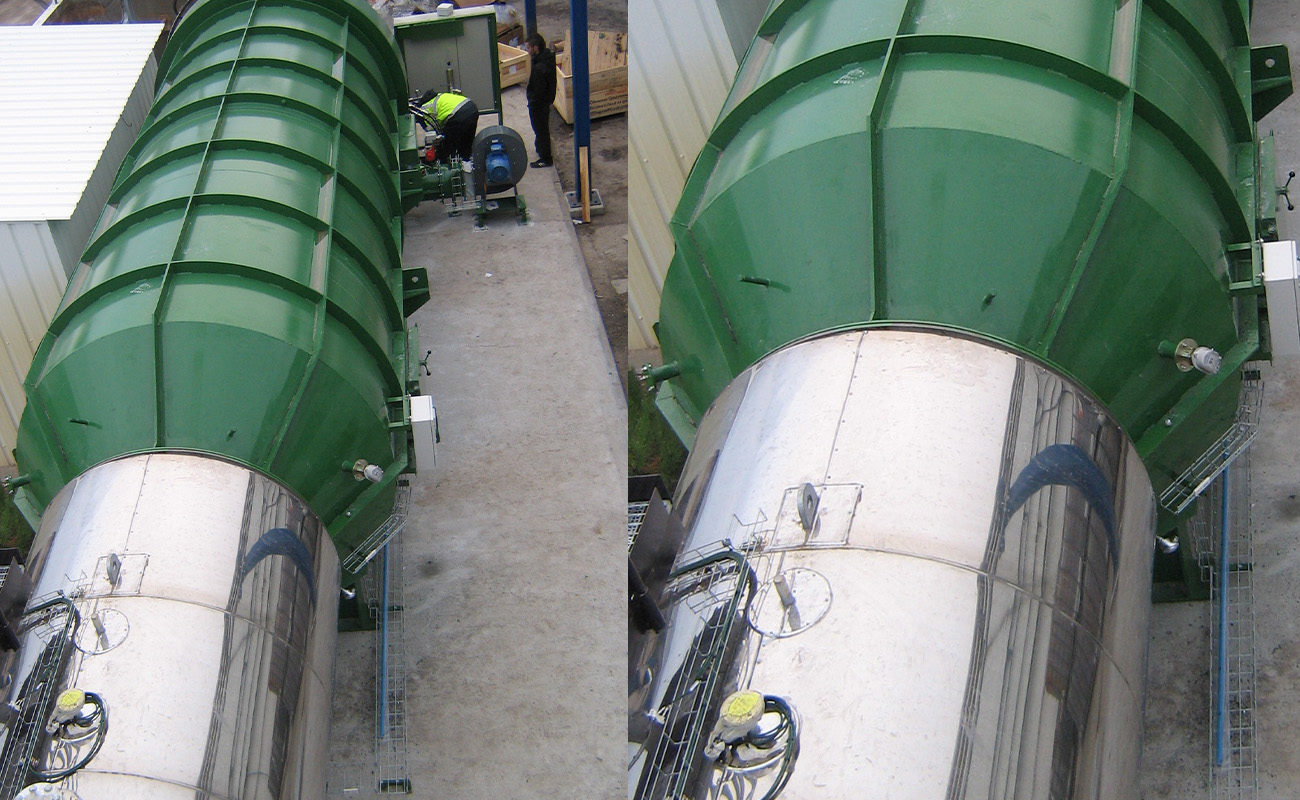
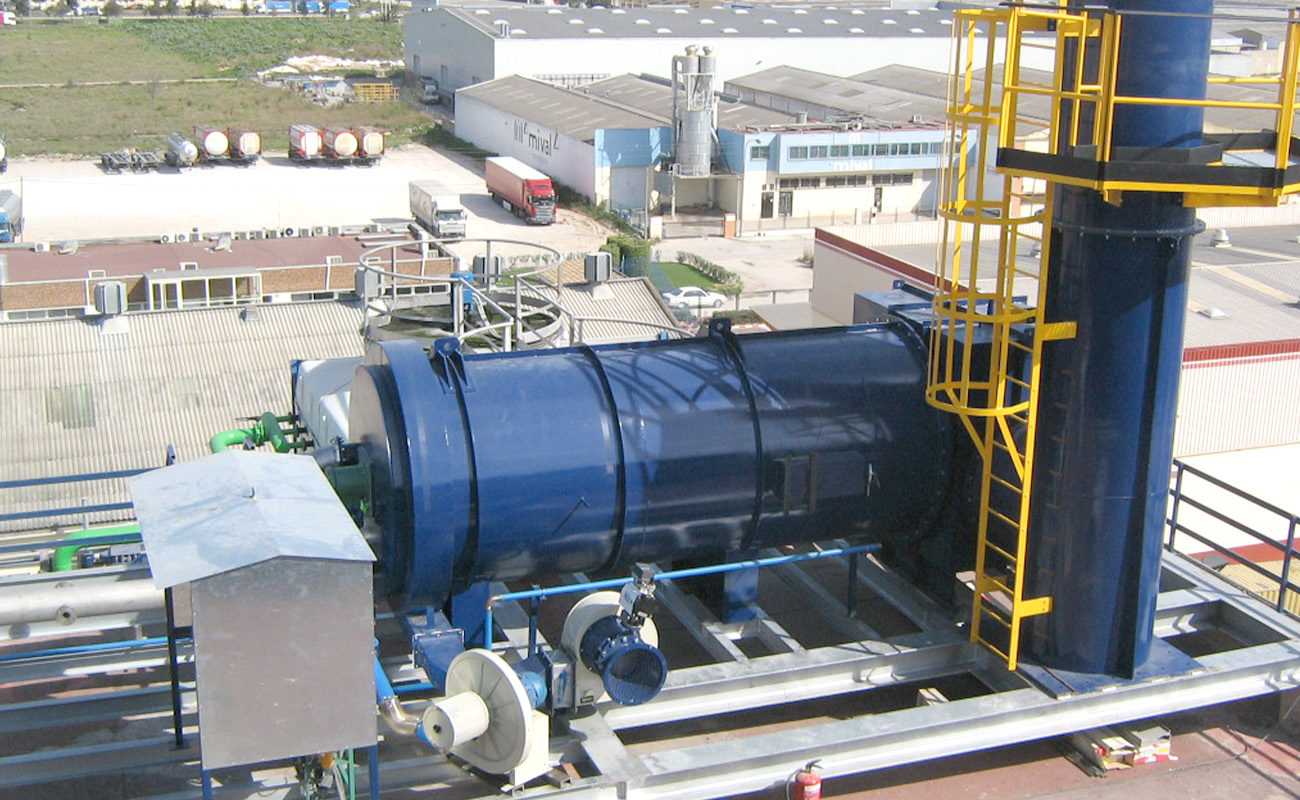
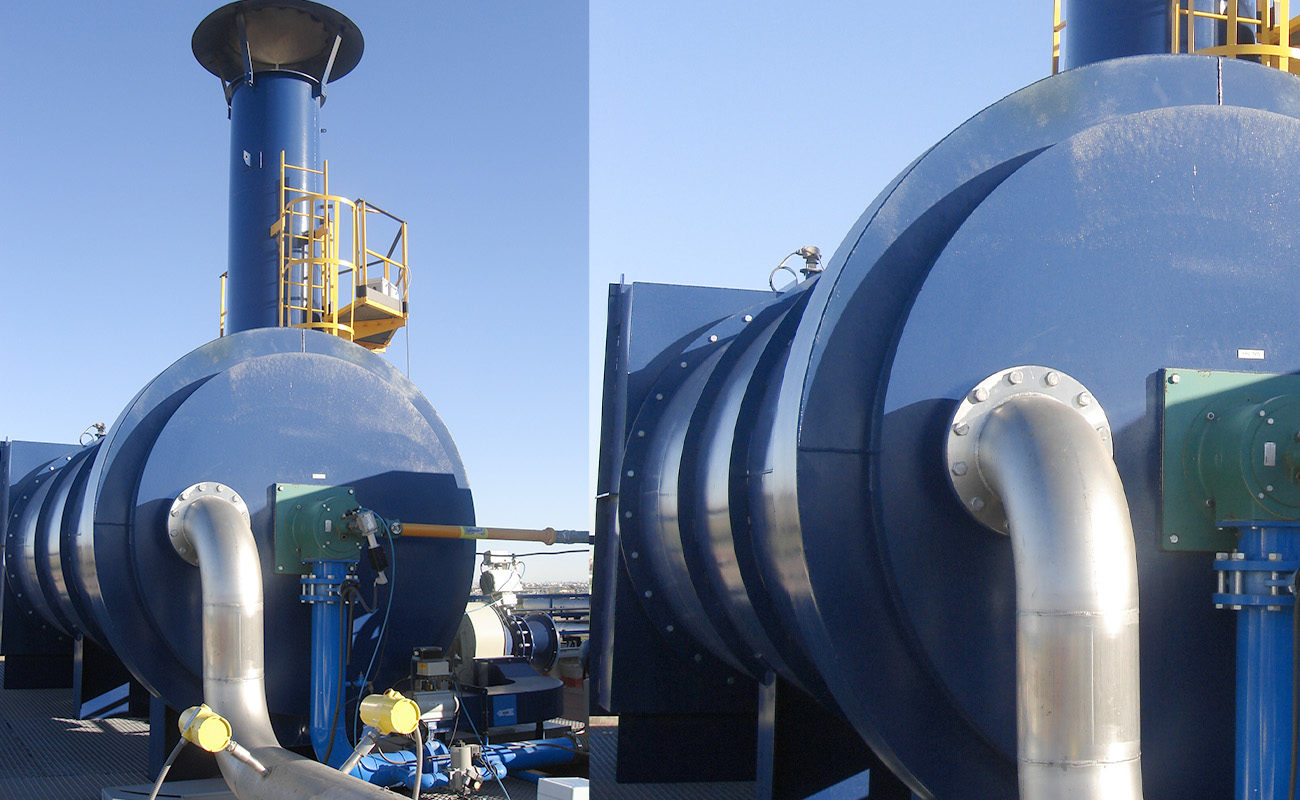
ELEMENTS THAT THE DEVICES HAVE
The oxidation chamber is made up of:
- Carbon steel oxidation chamber, insulated internally.
- Modulated natural gas, LPG or Diesel burner.
- Combustion air / ambient air fan for the excess oxygen necessary in the chamber.
- Chimney for releasing the output gases to the atmosphere.
- Heat recovery.
HEAT RECOVERY
Element used to take advantage of the heat existing in the output gases of the oxidation chamber. Types:
- Thermal oil heaters.
- Preheaters of gases to be purified.
- Process air heaters.
- Steam generators.
- Water heaters.
These elements contribute to minimising operating costs, as the energy resulting from this oxidation is used as thermal energy in the production process, reducing consumption of external energy.
This technique is suitable for eliminating both volatile organic compounds and inorganic compounds (CO, SH2, NH3, etc.) and in cases where the flow of gas is small (up to 40,000Nm3/h) and the concentration of the contaminant is high (from 4g/Nm3/h to 20g/Nm³).
EMISSIONS TREATMENT AND CONTROL